Delivering Safe, Compliant Cell Therapy Products
Our Cell Processing Facility (CPF) is a Good Manufacturing Practice, or GMP, bioprocessing manufacturing facility that supports the reproducible production of human hematopoietic or immune-competent cells under stringent quality control and safety requirements for therapeutic studies. Our CPF team aims to consistently deliver safe and compliant cell therapy products for Phase 1/2 clinical trials.
Located in the E level of the Thomas Building, the 3,700-square-foot, controlled-access facility consists of four separate suites designed for cell culture, material preparation and various clinical processing operations. The CPF is controlled by a building management system with an independent HVAC system maintaining ISO 7 specifications.
Schedule With Us
To learn more about collaborating with us, connect with our product management group. To inquire about a facility tour or to get more information about our CPF, please contact us at:
ON THIS PAGE
Virtual Tour | Our Products & Process | Equipment | Process Development | Product Management
Take a Virtual Tour
This virtual tour takes you inside the Therapeutic Products shared resource’s CPF to learn about the processes, facilities and equipment for producing high-quality cell products for clinical trials. Highlights:
- Gowning and degowning areas
- Four manufacturing suites
- Manufacturing processing equipment
- Materials control
- Quality lab
Go inside the CPF and learn about our work.
Our investigator clients provide us with the manufacturing production processes, which our process development group may develop further. Our process engineering group works with the investigator and/or process development to facilitate a process transfer, which ensures we understand the production steps in order to create the production batch records required for execution traceability.
Our materials control function ensures procurement, receipt, release and appropriate inventory of all goods and raw materials we need to produce GMP clinical product.
Our production scheduling function works with the clinic to coordinate product delivery and ensure all necessary process steps are appropriately scheduled and assigned.
We use quality assurance-approved standard operating procedures performed by trained, qualified personnel in accordance with cGMP. We are supported by the quality team to ensure regular compliance and safety of our therapeutic products.
All aspects of the CPF are maintained according to specifications set by Code of Federal Regulations title 21, sections 210 and 211, to meet current GMP (cGMP).
The CPF uses various biopharmaceutical manufacturing technologies to establish one-per-patient, parallel production of cellular therapeutic products. These technologies enable us to drive cost effectiveness, process efficiency and product consistency for the manufacturing process.
Cell production operations can include enrichment or depletion of specific cell subsets, provision of normal donor feeder cells, maintenance of transformed feeder cell lines, cloning, ex vivo antigen priming, cytokine and antibody-based activation, genetic modification, expansion, cryopreservation and/or preparation for infusion of many different types of extensively manipulated cell populations.
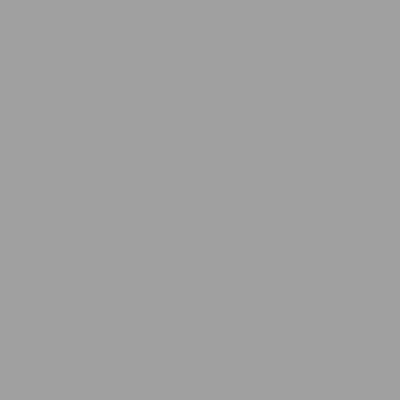

The manufacturing suites that support the production of cellular therapeutics are equipped with ISO 5 biological safety cabinets and numerous double stack Thermo Steri-Cult humidified CO2 incubators. Other major equipment includes floor and tabletop centrifuges, cell washers and large-scale cell enrichment devices.
This automated cell counter provides consistent cell counting and analysis using state-of-the-art image cytometry.

The blood cell counter uses fluorescence flow cytometry technology to provide complete differential blood count for all white blood cell populations.

This instrument automates cell separation for clinical enrichment of target cells or depletion of unwanted cells in a closed and sterile system.

The Prodigy is a closed system that offers automated cell processing capability, from cell separation through cell culture to formulation of the final product.

This microfluidics chip-based cell sorter features comprehensive fluidics controls, advanced automation and easy-to-use software.

The Sepax C-Pro is a closed and automated cell processing system (automated Ficoll) that uses single-use kits and custom software to automate multiple steps of the manufacturing process.

This automated, closed system washes and volume-reduces cell products through spinning membrane filtration.

This system delivers an automated, controlled expansion environment for the growth of cell therapies in volumes up to 25 L across research, process development and manufacturing operations.

The CryoMed controlled-rate freezers offer customizable freezing profiles.

Our LN2 storage system provides a cryogenic storage solution with high capacity to store 2 mL and 5 mL vials and cryobags.

Our process development team offers expertise is all key steps in the process of developing cell-based therapies in the CPF.
These steps include cell selection, flow cytometry, cell counting and washing technologies, cytotoxicity assays, formulation and cryopreservation, viral vector transduction (static and spin-fection) and analytic development. This support is required by the Food and Drug Administration for first-in-human Phase 1/2 clinical research studies.

Services:
Process development services include the following:
- Preclinical development to optimize product yield and functionality
- Improving process scale-up reliability and robustness
- Evaluating and testing cGMP-compliant materials and clinical-grade reagents
- Complying with requisite safety and release specifications
- Collaborating with manufacturing to produce standard operating procedures and batch records
- Performing pilot studies and validating key systems prior to process transfer to clinical manufacture
- Executing validation studies
- Supporting GMP manufacturing
- Providing Investigational New Drug, or IND, submission support
Our product management team owns the process we depend on to ensure your successful IND submission, GMP-compliant manufacturing and on-time delivery of high-quality product to patients.
Complete our new clinical trial intake form to initiate a new collaboration with us.
Drawing on industry-based technical knowledge, our product management team tracks key advancements in clinical cell therapies and emerging technologies at Fred Hutch, partnering with scientific, regulatory and business development teams to assess investigator-initiated therapeutic products and outside business opportunities.
For other information about how we can work with you, contact our Technical Product Management Director, Cell Therapy, Lara Kropp.
- Intake and Planning: Drawing on technical expertise and understanding of cell therapy cGMP manufacturing processes, our product managers assess capacity and feasibility of any new product with other Therapeutic Products shared resource team leaders. Working with clients, principal investigators, and clinical and regulatory partners, we develop a strategic and tactical plan for manufacturing and delivering product to patients. We review key predetermined workflow deliverables within established standard lead times and work with technical staff to identify and mitigate risks.
- Management of Deliverables: Our product managers establish a workflow by using the product life cycle (see below) and other strategic tools to manage deliverables for various cross-functional teams throughout the product life cycle and clinical trial.
- Communications: After our product managers establish the product life cycle workflow and identify priorities and timelines, we establish regular meetings with key stakeholders. At these meetings, PIs, partners, clients, regulatory and clinical personnel and the core’s own subject matter experts review progress on critical objectives, such as analytical methods, process development, engineering data run, change management, and IND section 7 (chemistry, manufacturing and controls, or CMC) authoring.
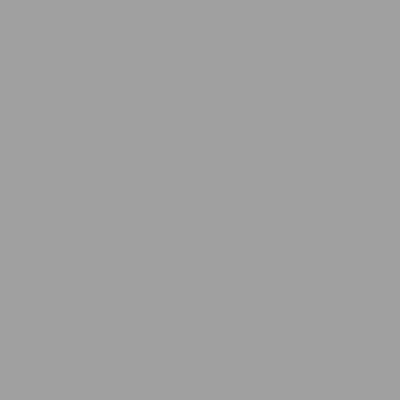
- Trial Inquiry and Intake: Upon receipt of the completed clinical trial intake form, we review the client’s timeline needs and conduct a feasibility assessment. If applicable, we conduct a tech transfer review.
- Project Plan and Scope of Work: We develop the project plan which includes an initial gap assessment, scope of work and associated timelines. The project team is then assembled.
- Process Development and Process Transfer: Our process development team evaluates the manufacturability and scalability of the proposed product. Our process engineering team transfers the process to the manufacturing facility, and we develop batch records, the bill of materials, analytical test methods and other critical documents.
- IND-Enabling Confirmatory Production: In support of the IND application, we execute the developed, finalized manufacturing process within our cGMP CPF to specification.
- CMC Package Submittal: We support the drafting and finalization of the IND section 7 CMC and compile the IND-supporting CMC data package.
- Clinical Manufacturing Readiness: We finalize critical documents, complete materials procurement and conduct operator training.
- Trial Open & Full Product Delivery: Our product management team continues to monitor and evaluate product delivery. The team also supports the implementation of necessary modifications to ensure compliance and quality product delivery to patients for the duration of your trial. Product managers also host biweekly or monthly meetings to connect you with our technical teams and facilitate ongoing collaboration.
- Completion of Study Cohorts: Upon trial completion, our product management team coordinates the closure of the study and the transfer of data and any residual generated material to the PI for further research.